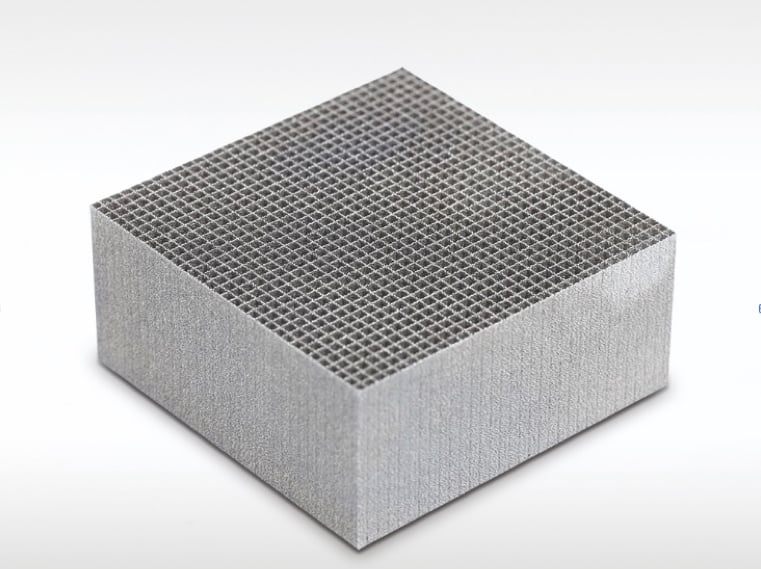
A 3-D printed tungsten pre-clinical X-ray system collimator. The tungsten alloy powder is printed into the form desired and is laser fused so it can be machined and finished. Previously, making collimators from Tungsten was labor intensive because it required working with sheets of the metal to create the collimator matrix.
In molecular radiotherapy (MRT) treatment of the thyroid, existing single photon emission computed tomography (SPECT) imaging systems are unable to accurately measure radiation absorbed by patients during and after treatment. As a consequence, only limited information regarding the success of radiotherapy treatment has been available.
For the last six years, teams from the University of Liverpool’s Department of Physics and The Royal Marsden and Royal Liverpool University Hospitals have been working to develop an imaging system (known as DEPICT) that would better measure the absorbed radiation dosimetry. The aim is to provide a more accurate treatment and diagnosis of patients.
Central to the imaging system’s scanner is a collimator. This is a device which aligns the beams of radiation emitted from the patient so that they are directed onto a detector. The radioactive iodine is ingested by the patient in liquid or capsule form, and then gamma rays are emitted in all directions through the patient, yet only the rays which are aligned with the collimator holes will make it through to the detector. The data received can then be converted into an image on a computer screen.
Previously, lead was the preferred material for collimators. However, tungsten is much more efficient than lead at screening unwanted gamma beams. Additive manufacturing now allows the collimators to be made in tungsten, resulting in much clearer images of the radiation dose received by the patient.
A critical part of the new imaging system is the use of a direct-digital conversion, cadmium-zinc-telluride (CZT) detector. This part is used in conjunction with a parallel hole collimator with an active area comprising an array of 0.6 mm holes. Traditionally made of lead, collimators on the market were not up to the task of supporting the new DEPICT system, because it required a very intricate design that was not possible to create from this relatively soft material. Researchers hit on the idea that high-density tungsten could be the ideal material if they could find a way shape it into the required collimator.
Tungsten Difficult to Work With, But Ideal For Collimators
Tungsten’s density is around 1.7 times that of lead traditionally used in collimators, but it is difficult to work with because it has the highest boiling and melting points of any element known to man. It also means there is no other material in the world capable of holding tungsten as a molten liquid, so it cannot be cast into high precision shapes in the manner of iron, aluminum and other common metals. That is until now.
A group of experts in the U.K. recently began 3-D printing of intricate geometrical shapes from tungsten alloy powder as a new method to work with material. A team from Wolfmet, a company that makes components for automotive and aerospace, developed this highly specialized additive manufacturing metallurgy process, essentially fusing the tungsten alloy powder together. A high-powered laser is applied to fuse successive layers of pure tungsten powder until a complex component is built. Once fused, the powder is pressed into parts, sintered and then machined into the desired form.
The Wolfmet tungsten team has developed a highly specialized metallurgy process, essentially fusing successive layers of tungsten powder to build a finished component.
The method is ideal for the manufacture of high-precision components such as collimators and radiation shields in CT, SPECT, MR and X-ray imaging systems. Furthermore, the technique allows components to be produced cost effectively in days and weeks rather than months.
The technique, also called selective laser melting (SLM) or direct metal laser sintering (DMLS), is an additive manufacturing technique which, for the first time, enables the production of individual metal components with complex geometries without the need for part-specific tooling. The additive manufacturing process uses the high energy laser to shape the layers of metallic powders to form three-dimensional components.
The geometries that can be achieved are not possible using traditional machining, otherwise known as subtractive manufacturing. By removing this design limitation, the possibilities are almost endless. When tungsten’s excellent radiation absorption combined with good thermal resistance is added into the mix, the possibilities become genuinely exciting.
The end material is an alloy, of 90-97 percent tungsten depending on the grade. This material retains the unique density and radiation shielding capabilities of pure tungsten however, for the first time, it can also be machined to tight tolerances.
Creating a Complex 3-D Printed Collimator
The team at Wolfmet helped create the world’s first collimator of its kind for the DEPICT system. After undergoing recent trials, the group reported great success. With its excellent attenuation properties, a tungsten collimator significantly reduces septal penetration in comparison with the same collimator made from lead, resulting in much improved image quality.
“The final product shows great potential to enable better radiotherapy treatment monitoring,” said Samantha Colosimo, Ph.D., project manager, Optimization of Medical Accelerators (OMA) Project, University of Liverpool.
The team working on the project is hopeful that the DEPICT imaging system will be available commercially in the next three years.
The implications could be significant; the ability to individualize treatments is expected to reduce healthcare costs by providing speedier and more efficient treatments. Importantly, it is hoped that this development will increase rates of successful cancer treatment, leading to improved quality of life and health for those patients.
Applications Outside of Healthcare
The same principals of 3-D printing tungsten could mean huge advances in other sectors outside of healthcare.
Airport and cargo scanners used to examine the contents of transport containers could be upgraded in the same way using tungsten collimators. The scanners often have tungsten grids that screen out stray X-ray beams to give a more accurate image. These grids are currently built up manually from many individual tungsten sheets, but could soon be replaced by monolithic SLM parts.
The application of the metallurgy process allows these complex parts to be manufactured as a single component. This results in a much shorter delivery time and eliminates a lot of costly hand assembly work.
The geometrical detail, which can be incorporated into the tungsten, could now mean that increasingly complex components can be created. In the future this means it may be possible to provide handheld, lightweight medical scanners that can be used to home in on individual organs while producing similarly accurate images.
Tungsten properties are well known, but only now can they be harnessed more fully through this new manufacturing method.
Steve Jeffery is the business development manager for Wolfmet's 3-D printed tungsten components division.